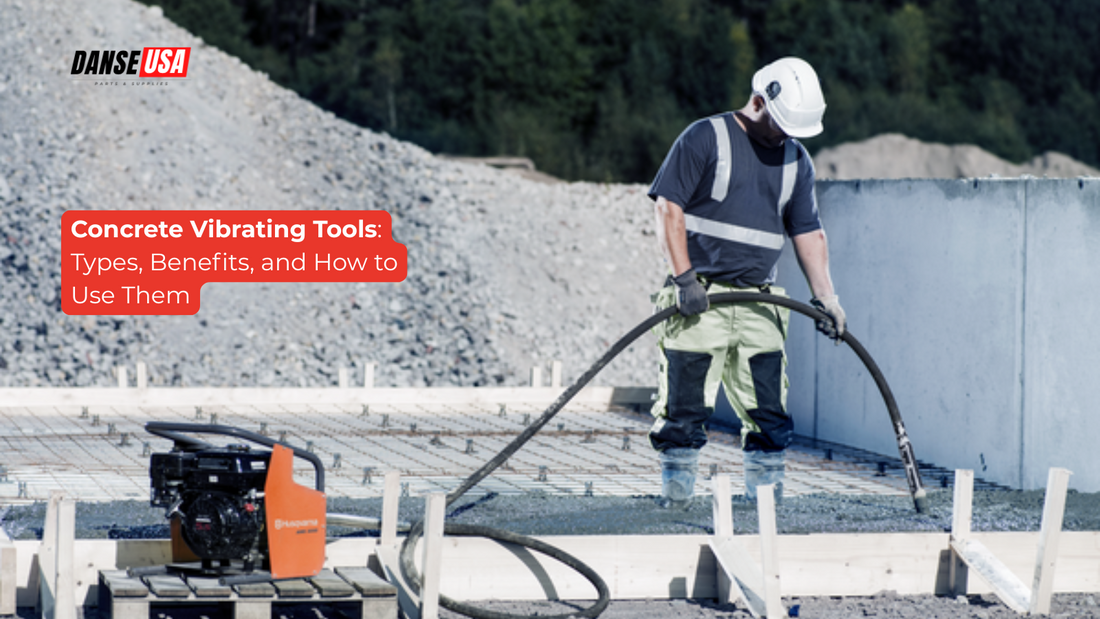
The Ultimate Guide to Concrete Vibrating Tools: Types, Benefits, and How to Use Them
Share
When working with concrete, achieving the right density and strength is crucial for structural integrity and long-term performance.
While pouring and finishing concrete gets much of the attention, one of the most critical — and often overlooked — steps in the process is vibration. This is where a concrete vibrating tool comes in.
Concrete vibrators are essential equipment on any job site where concrete is poured. These tools help remove trapped air and excess moisture, allowing the concrete to settle fully around reinforcing bars (rebar) and into formwork.
If you've ever seen a concrete surface riddled with holes, weak edges, or premature cracks, chances are proper vibration was skipped.
In this blog post, we'll explore everything you need to know about concrete vibrating tools, including their types, applications, benefits, operation tips, maintenance, and safety precautions.
What is a Concrete Vibrating Tool?
A concrete vibrating tool, also known as a concrete vibrator, is a mechanical device that emits rapid vibrations into freshly poured concrete.
These vibrations cause the concrete particles to consolidate, displacing air voids, helping the aggregate settle, and ensuring a uniform, dense structure.
In freshly poured concrete, up to 20% of the volume can be made up of air voids if not properly vibrated.
These voids compromise strength, reduce bonding with steel reinforcement, and leave unsightly surface defects. By using a concrete vibrator during placement, contractors can:
-
Increase compressive strength
-
Minimize the risk of honeycombing
-
Improve surface finish
-
Ensure full formwork coverage
Whether you're building a skyscraper, a driveway, or a simple concrete patio, a vibrating tool can make or break the quality of your structure.
The Importance of Concrete Vibration
1. Eliminates Air Pockets
Concrete is a mixture of cement, aggregate, sand, and water. During placement, it often traps air, which can cause internal voids. Vibration helps release these air pockets, especially around rebar and corners.
2. Increases Structural Integrity
Proper compaction significantly increases concrete’s compressive strength. Poorly vibrated concrete may suffer from lower durability, leading to premature failures, spalling, or cracking.
3. Prevents Honeycombing
“Honeycombing” refers to the visible voids or rough patches on concrete surfaces due to incomplete filling. Vibrators ensure a smooth, monolithic pour that conforms to the mold.
4. Enhances Bond with Reinforcement
Concrete must tightly encase steel bars to prevent corrosion and support load transfer. Vibration ensures the mix fills every gap and adheres to rebar.
Different Types of Concrete Vibrators
Choosing the right type of vibrator depends on the application, the size of the pour, and access to the concrete. Let’s break down the main types.
1. Internal Vibrators (Needle or Poker Vibrators)
-
These are the most commonly used vibrators.
-
A long, cylindrical head (the needle or poker) is inserted directly into the wet concrete.
-
Operated by electric, gas, or pneumatic motors connected via flexible shafts.
Applications:
-
Foundations, walls, slabs, columns, beams
-
Best for deep pours or congested reinforcement areas
Advantages:
-
Direct, efficient compaction
-
Multiple head sizes for various job types
Limitations:
-
Manual labor required to insert and withdraw
-
Risk of segregation if misused
2. Formwork Vibrators (External Vibrators)
-
Mounted to the outside of formwork
-
Indirectly vibrates the concrete through the mold
-
Often used in precast facilities or when internal access is limited
Applications:
-
Precast panels, tunnel linings, slender columns, complex molds
Advantages:
-
Non-invasive to the concrete
-
Ideal for architectural finishes
Limitations:
-
Less effective on thick pours
-
Requires strong formwork to handle vibration
3. Surface Vibrators (Screed Vibrators)
-
Operates on the top surface of the pour
-
Often used as part of a screeding system that levels and finishes the surface
Applications:
-
Pavements, slabs, parking lots, floors
Advantages:
-
Compacts and levels in one operation
-
Speeds up large flat pours
Limitations:
-
Only affects top layers (up to 6 inches deep)
-
Not suitable for vertical elements
4. Table Vibrators
-
Stationary vibrating tables used in controlled environments
-
Common in precast concrete production
Applications:
-
Tiles, pipes, blocks, decorative elements
Advantages:
-
Uniform vibration
-
Reduces labor
Limitations:
-
Limited to factory environments
How to Use a Concrete Vibrating Tool Correctly
Proper technique is essential for maximizing the benefits of vibration. Here are some professional tips:
Step-by-Step Guide:
-
Plan your vibration path: Use a systematic grid to cover the entire pour.
-
Insert the needle vertically: Do not push in at an angle as this may create voids.
-
Vibrate for 5–15 seconds per spot: Depends on slump, vibrator size, and pour depth.
-
Don’t overdo it: Excessive vibration can cause segregation — when heavy aggregates sink and water rises.
-
Withdraw slowly: About 1 inch per second to allow the concrete to fill the void left by the needle.
Recommended Spacing:
-
Insert the vibrator every 12–18 inches
-
Overlap the radius of vibration (typically 6–12 inches depending on tool size)
Signs of Proper Vibration:
-
Concrete flows into place around the vibrator
-
Surface becomes glossy as water rises
-
Air bubbles rise and burst
Safety Precautions
While concrete vibrators are not particularly dangerous, safety should always come first.
PPE You Should Wear:
-
Gloves to reduce vibration impact and protect hands
-
Eye protection against splashes
-
Ear protection, especially with gas-powered units
-
Rubber boots for wet environments
Operational Safety Tips:
-
Avoid contact with rebar while vibrating — can cause electrical conduction or damage the tool
-
Use insulated tools in wet areas to prevent electric shock
-
Take breaks when working long hours to avoid hand-arm vibration syndrome (HAVS)
-
Use both hands and maintain balance while operating
Maintenance Tips for Long-Term Use
Like all construction equipment, concrete vibrators require regular upkeep.
After Every Use:
-
Clean immediately to prevent hardened concrete buildup
-
Inspect for wear — look at the needle head, hose, and motor
-
Lubricate bearings and shafts if applicable
-
Check power connections for damage or moisture intrusion
Periodic Checks:
-
Replace worn poker heads and shaft cables
-
Tighten any loose bolts or couplings
-
Run the motor before each job to ensure functionality
Storing the tool in a dry, sheltered place will extend its lifespan significantly.
Choosing the Right Vibrator for Your Project
To select the right concrete vibrator, ask yourself:
-
What’s the depth of the pour? For deep pours, use internal vibrators.
-
Is it precast or cast-in-place? External or table vibrators may be better for precast.
-
Is the formwork fragile or decorative? External vibration avoids disturbing the mix.
-
What power source is available? Choose electric, pneumatic, or gas based on the job site.
Here’s a quick comparison:
Application | Recommended Type | Power Source |
---|---|---|
Foundations | Internal vibrator | Electric or gas |
Slabs & Pavements | Screed/surface vibrator | Electric |
Precast Forms | External or table vibrator | Electric |
Remote Sites | Gas-powered needle vibrator | Gasoline engine |
Common Mistakes to Avoid
-
Skipping vibration on small jobs: Even patios or sidewalks benefit from compaction.
-
Vibrating too long: This can lead to bleeding, segregation, and a weak surface.
-
Using the wrong size needle: Small needles don’t work efficiently in large pours, while large ones may damage forms.
-
Not overlapping vibration zones: Leads to inconsistent compaction.
Final Thoughts
Concrete vibrating tools are a critical component of any high-quality concrete installation.
From residential slabs to industrial columns and precast panels, proper vibration ensures your concrete is strong, dense, and free of defects.
Whether you’re a DIY enthusiast pouring a backyard walkway or a commercial builder managing large-scale projects, using the right type of concrete vibrator — and using it correctly — can save time, reduce costs, and deliver superior results.
Invest in quality tools, follow best practices, and never skip this essential step in the concrete process.